Communities in multiple states are already increasing the performance as well as sustainability of their pavement with high-level blends of reclaimed asphalt pavement (RAP). Cargill supplies the biobased Anova rejuvenator that allows for the use of high-RAP content and offers a rapidly renewable ingredient. New multi-year national trials offer performance-based evaluations for road decision makers.
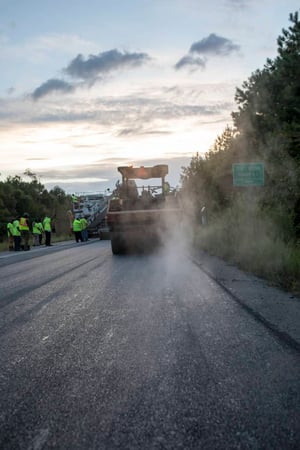
Soybean oil is an abundant and quality ingredient, offering performance as well as renewable content. Cargill’s biobased road innovation is paving new markets for U.S. soybean farmers by creating demand for the oil of soybeans that remains after the meal is processed from the crop for human and livestock feed. Rapidly renewable by nature, biobased products like Cargill’s benefit the economy, create jobs, and reduce dependence on fossil-based oil.
Neumann said that results from the multi-year NCAT and MnROAD trials will help state agencies gain confidence in performance-based testing. As part of the project, the researchers will compare blacktop made with Cargill’s Anova rejuvenator in a 45 percent RAP mix to control sections paved with a lower RAP mix without the Anova rejuvenator, measuring factors such as pavement ride quality, cracking and rutting. By conducting parallel testing at both the NCAT test track and MnROAD test highway, scientists will be able to monitor results in both northern and southern climate extremes.
Mix design began earlier this year, as researchers from both facilities conducted extensive laboratory analysis on pre-construction samples. In early September, NCAT paved 200-foot-long section of its 1.7-mile oval pavement test track with the Anova/high RAP mix. There, scientists are evaluating the performance-engineered asphalt mix using an accelerated pavement testing protocol, subjecting the section to 10 million equivalent single-axle loads (ESAL) or about 10 years’ worth of traffic, in only two years. The NCAT test is conducted in cooperation with the Virginia Department of Transportation.
Paved in early October, the MnROAD project covers two approximately 500-feet sections of the test highway. It’s being done in conjunction with the Minnesota Department of Transportation, which owns and operates the testing facility, and CRH/Hardrives. Both test locations will conduct ongoing laboratory testing and field monitoring as they work to utilize various performance-engineered design protocols, while also assessing potential practical quality control tests that can be used when constructing pavements using such designs.
“We know many state agencies are looking for advances in asphalt that deliver demonstrable performance benefits,” said Hassan Tabatabaee, global technical manager for road construction, Cargill. “With this research, we’ll be able to equip state agencies with well-controlled, real-world data on new design principles, especially when used with rejuvenators and high RAP mixes, giving them greater confidence in adopting these research-based quality control tests.”
The push for new performance-based evaluations comes as the industry faces growing pressure to increase infrastructure sustainability, while managing costs and improving durability. High RAP mixes, made possible by advances in rejuvenator technology, offer the potential to address all three of these key concerns.
UP TO 100% RAP
Cargill’s Anova rejuvenator is specifically designed to rebalance aged asphalt and enable the recycled material to perform similar to virgin material. As a result, it’s possible to increase the amount of recycled content in the asphalt mix from today’s typical 22 percent RAP mix, up to 50 or even 100 percent RAP, without sacrificing performance or durability.
According to Cargill, increasing the recycled content by just 20 percent on a typical 5,000-ton resurfacing project saves 48 trucks of virgin aggregate, 1,000 tons of recycled asphalt storage costs, two trucks of liquid asphalt, along with the carbon emissions generated by all those trucks. However, while these rejuvenator/high RAP asphalt mixes deliver on critical sustainability, cost-management and performance criteria, they don’t always meet long-standing, ingredient-based requirements.
“Rather than relying on a specific ‘recipe’ to deliver performance, we need to be evaluating our asphalt mixes based on measurable factors like durability and workability,” Tabatabaee said. “Developing and adopting research-based quality control practices will enable agencies to speed adoption of innovations like high RAP/rejuvenator mixes, providing them with reliable data to more effectively evaluate new technologies based on actual results.”